Czech Republic attracts new companies to lower operating costs - energy price is not the key factor, but its savings are
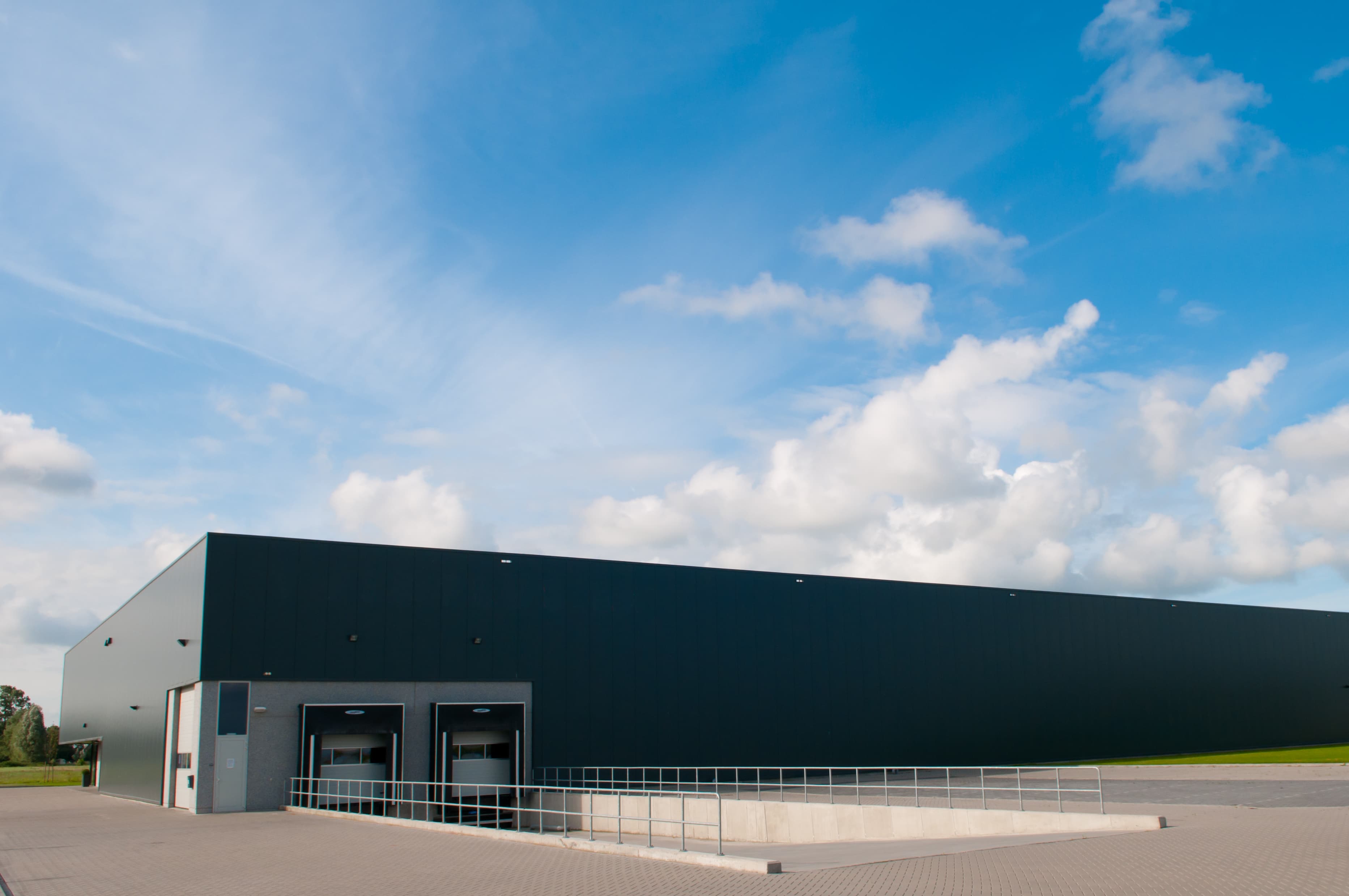
Location, price, transport accessibility, labour availability and up to 5th place energy performance / sustainable building certification. These are the main criteria for companies when selecting warehouse space. This was shown by the results of the Trends in Czech Logistics survey conducted last year by the SKLAD association in cooperation with Ipsos. According to the real estate consulting company 108 REAL ESTATE, preferences are very similar in the case of the production space segment. However, despite the survey results, it turns out that it is the costs associated with the operation of industrial real estate that have a great influence on the success of the Czech Republic's offer in international tenders of global tenants.
As the industrial team at 108 REAL ESTATE has long pointed out, it was the costs associated with leasing industrial properties that weakened the Czech Republic's position in tenders from large logistics operators. Many companies chose the more affordable Poland as their location. In this respect, the situation started to change at the end of last year, also with regard to the growth of wage costs of Polish workers and other cost items.
The greater flexibility of domestic landlords regarding operating fees also played a role. These currently amount to EUR 0.5 to 1.5/m²/month, with a very high share - around 20% - of security costs.
"Those who want the comfort of physical security are prepared to pay for it. On the other hand, however, it is possible to reduce the cost of security, for example, by connecting the building to the central security desk of the Fire Brigade," explains Petr Jílek, head of the property management team at 108 REAL ESTATE, which currently manages about 250,000 m2 of rentable space.
However, there are items that cannot be saved within the operation. For example, tenants of logistics complexes insist on flawless snow clearance during the winter, while in the case of production, a guarantee of a constant supply of electricity or stable temperature is very often required. In this respect, new modern buildings have an advantage, where, despite higher rents, there are lower costs associated with the inspection and revision of electrical wiring and the technical equipment of buildings in general, including air conditioning.
The amount of the service charge also depends on the specific requirements of the tenants. While manufacturing companies often require round-the-clock technical support, warehouse tenants are more flexible in this respect.
On the other hand, most companies do not address energy costs individually - they do not place emphasis on the possibility of choosing their own electricity, water or gas suppliers.
"They are more interested in the building's energy performance certificate than whether the building has a local distribution system, i.e. an LDS, which allows the tenant to contract the electricity supply directly. This is also due to the fact that energy suppliers are tendering less than in the past because the current situation on the electricity and gas market encourages spot price contracts. The distribution component of the price is given and the commodity changes for all traders equally. Therefore, the differences in offers are only minimal and only larger customers will achieve more significant savings," Petr Jílek shares his experience.
However, owners and tenants of industrial buildings attach considerable importance to energy savings. A key element is quality insulation of buildings, especially in the glazed parts, including skylights, where the greatest heat leakage occurs through thermal bridges. In logistics centres, where the temperature is kept between 12 and 15 °C in winter, heat loss is most often due to non-compliance with operational guidelines: for example, air curtains are not used at docking bays, where metal bridges for cargo and unloading can freeze to -10 °C. In similar cases, the thermal comfort inside the halls is not helped by additional heavy insulation of the façade and roof.
The installation of renewable energy sources is not a universal solution for reducing costs. Although some companies directly require these alternative technologies, their effectiveness depends on the nature of the operation.
"The combination of heat pumps, photovoltaics and battery storage is particularly worthwhile in manufacturing plants with continuous operation. Logistics facilities often generate excess energy that must be sold back at low prices. Efficient energy storage therefore becomes a key factor. As this technology improves, the willingness of companies to invest in renewable energy will also increase," explains Petr Jílek.
As SKLAD points out in its study, the key trends in industrial construction aimed at improving sustainability and efficiency can be expected to continue in the coming years. There will be a growing emphasis on building certification to confirm environmental standards and reduce carbon footprint. Reducing energy intensity will remain a priority, not only through the installation of renewable energy sources such as photovoltaic systems, but also through energy efficient technologies. Space optimisation will focus on greater flexibility and efficient use, supporting the trend towards automation that will reduce operating costs and increase competitiveness.
"The outlook for the next few years will be marked by sustainability, with major renovation of older buildings. Where renovation cannot achieve the desired condition, we expect demolition and construction of new buildings. At the same time, we will start to see more and more multi-storey buildings using industrial land more efficiently, which has been in short supply for a long time and is becoming more and more expensive," believes Matěj Indra, Head of Industrial Agency, 108 REAL ESTATE